Waste to Worth Tour Piques Interest in Nebraska Replication
In April, I traveled to Ohio to attend the Livestock and Poultry Environmental Learning Community’s Waste to Worth Conference. It’s a great conference for people like me – you know, the ones that really love to talk about manure. The conference is geared toward folks working in the manure education and research realm, so there’s a variety of manure educators, researchers, and professors as well as NRCS and regulatory personnel in attendance. I always enjoy going to this event because it’s a great time, full of lots of poop jokes, manure swag, and good friends. Plus, we manage to learn a lot from each other while we’re there. A highlight of this year’s conference is that the first day we all got to tour area farms and businesses that are doing great things with manure or other waste products.
Of the 3 possible day-long tours, the one I chose focused on composting. The first stop was a family-owned and -operated Ohio EPA Class 2 composting facility. The Andre family, who operates the facility, started by composting manure and animal feed waste, but now they also take in human food waste to be composted, rather than sending it to the landfill. Their main carbon source is still animal feed waste from a nearby dairy farm. Trucks full of biodegradable refuse of all kinds come in regularly from across the region.
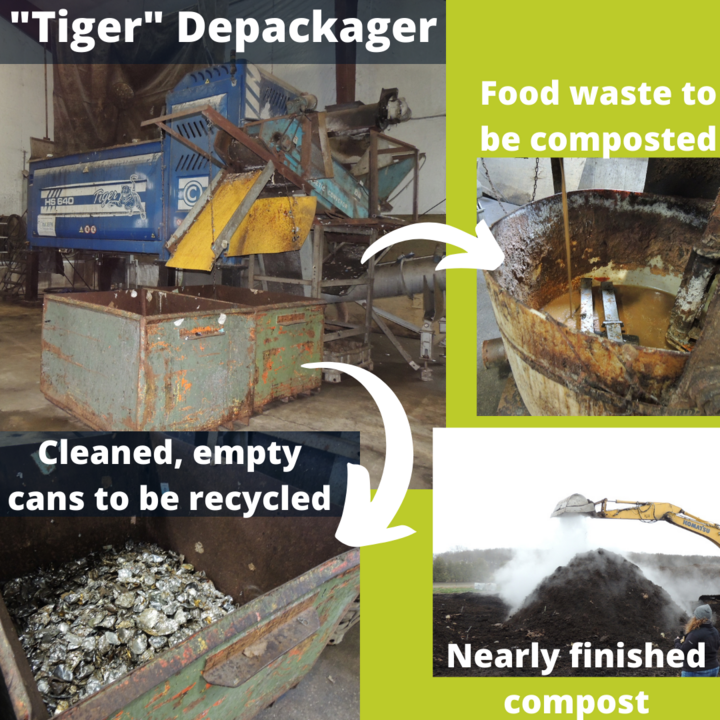
Prior to our arrival, the facility had received a load of pallets containing unsellable cans of soup, so they crushed some while we were there to demonstrate the machine. The soup came out one auger, the cans came out another conveyer after having been cleaned with recycled water from their holding pond (where all runoff from the composting facility is held). I have to say, it was a spot-on facility to tour around Earth Day.
At another site, we met a beef producer and farmer named Aaron, who was involved with a Great Lakes Commission grant led by Eric Richer, a crops-focused Extension Educator with Ohio State University Extension. The purpose of the grant was to find ways to decrease the volume of manure that needed to be hauled to the field, thereby making it more likely that farmers could haul the manure further to fields that needed the nutrients, rather than those closer to the livestock operation. The primary way of doing this was by composting the manure from his bedded beef barn.
While Eric and Aaron had access to a compost turner to make very consistent compost, traditional composting is rather time/labor intensive as the pile must be turned regularly to keep the compost internal temperature high enough. Aaron was quite innovative; he had an idea to try static composting and was successful. Using a 4” PVC pipe with a bunch of holes drilled in it and hooked up to a small squirrel cage fan, he tried static pile composting. He laid out the pipe horizontally and covered it in woodchips to keep manure from getting into the pipe, and then he stacked the manure on top of the pipe in a pile about 8 feet tall.
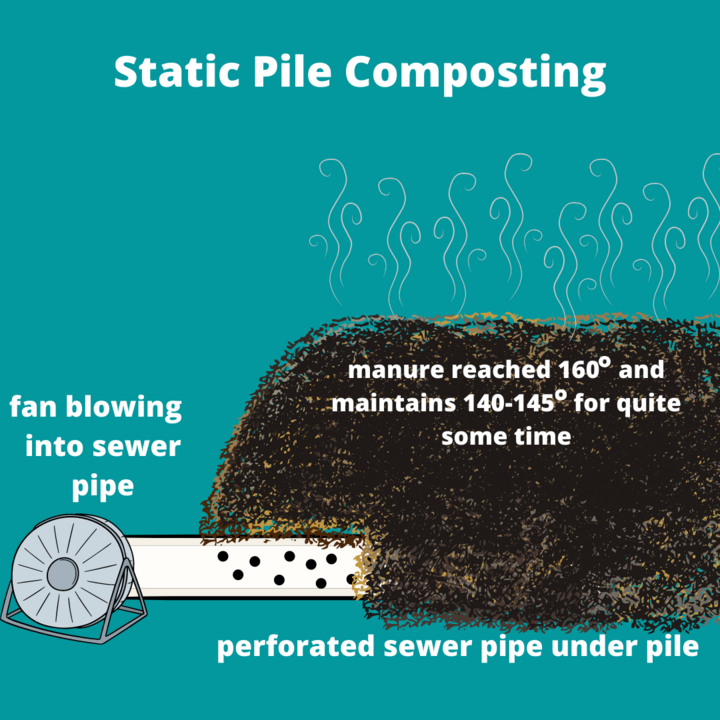
After the static composting worked so well, Aaron thought that maybe he could put some of the heat created with the compost to work. He built one of the static piles in a concrete bay outside his shop. While building the pile, he used coils of PEX tubing (plumbing pipe) to create a radiator of sorts throughout the manure pile. He then hooked up the PEX pipe to small pump and radiator and filled it with water inside his shop. He rigged an old box fan to pull the heat from radiator to warm his shop. It was very creative and kept his shop about 50 degrees for a good portion of the winter.
One thing I observed was that Aaron was using woodchips to bed his cattle. But that’s not as common here in Nebraska because woodchips aren’t as accessible as in Ohio. Still, this demonstration really got my creative juices flowing as I was considering how could we use what I was learning back home? I personally would love to see if static-pile composting works with manure that contains cornstalk bedding, which is more common here. If you would also be curious to try something similar maybe, we can partner up to do a little testing of this process here in a drier climate with cornstalk bedding rather than woodchips! Contact me to hear more about the tour, my experiences at Waste to Worth or if you're interested in trying composting out yourself.
This article was reviewed by Eric Richer, Extension Educator with Ohio State University Extension and Mara Zelt, University of Nebraska Research Technologist.